Risk can be defined as the possibility that an event could adversely affect the achievement of an objective. Automating precision solutions is, in and of itself, a process of identifying, managing, and reducing risk for our clients. The “problem” isn’t taking on risky projects, but is in taking on challenging projects while actively managing the risk profile. For this reason, DWFritz takes a very methodical approach to risk management through early identification, evaluation, and prioritization – then we constantly refine it. Risk management is an iterative process.
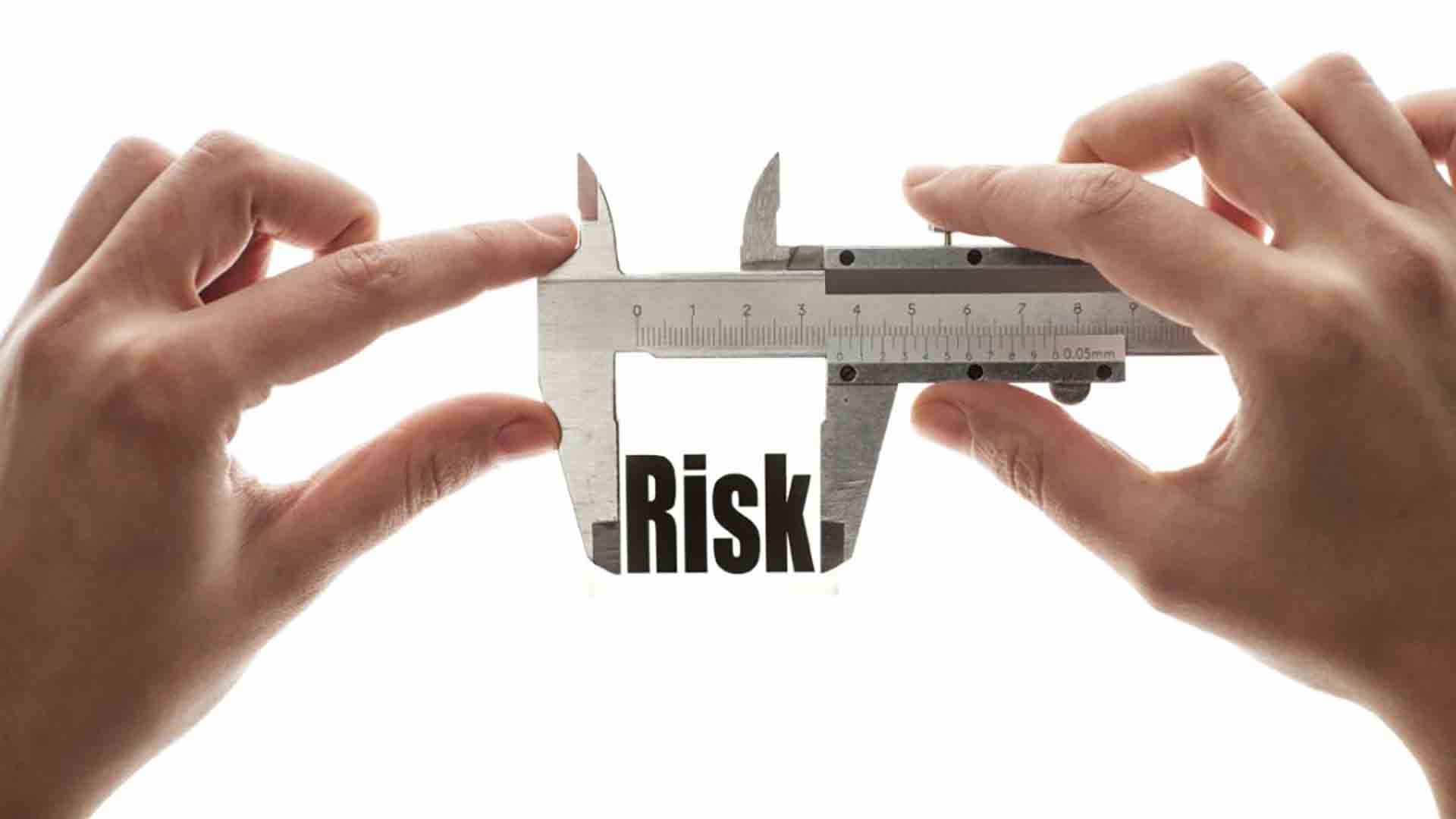
Ignoring the relevance of partnering with precision automation experts with risk mitigation expertise can greatly improve the productivity of teams, increase cost-effectiveness, profitability, quality, brand value, and future revenue. By identifying the probability of occurrence and impact, risks can be methodically prioritized and addressed through the risk register.
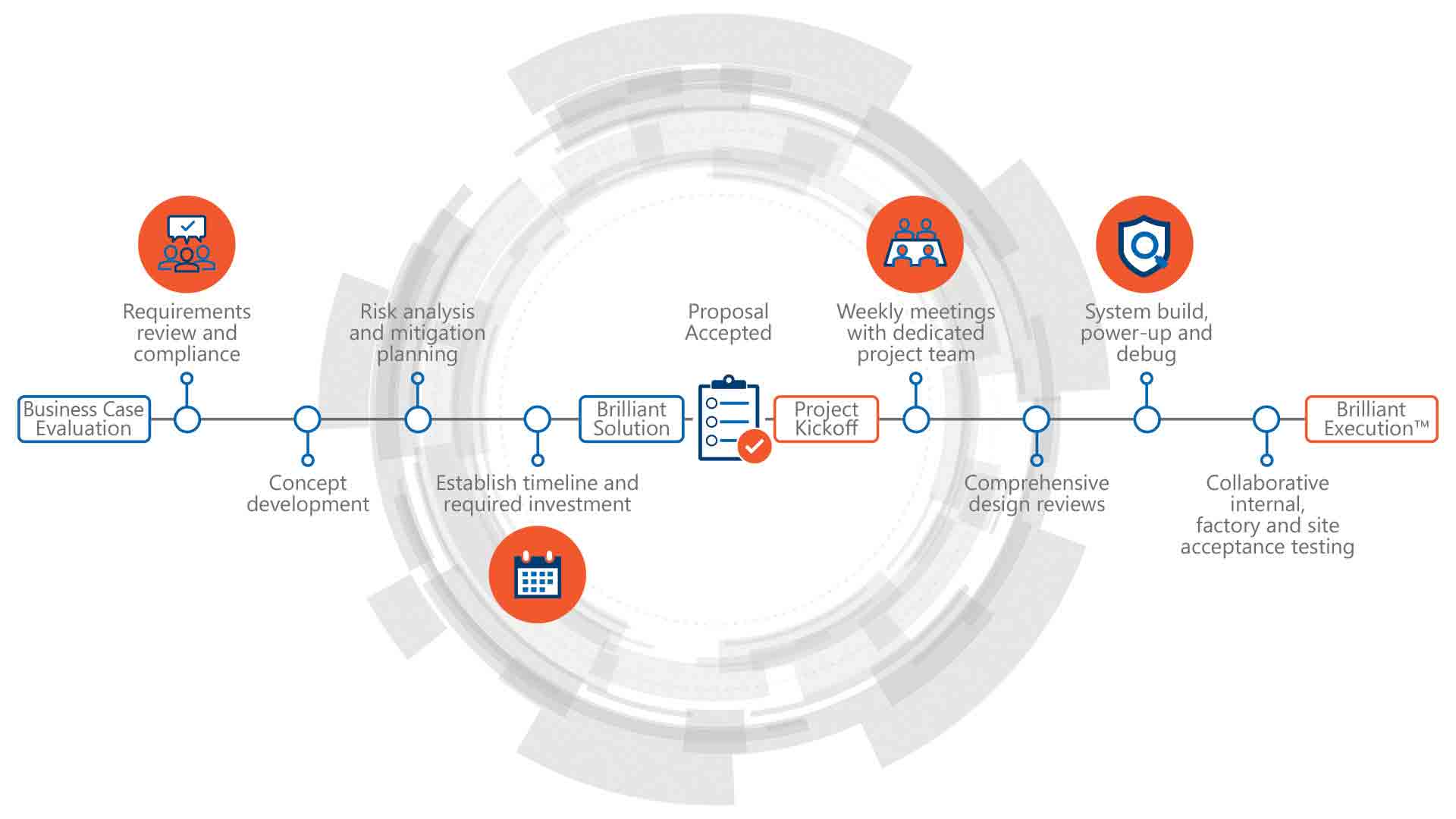
Step 1: Identification
When developing precision automation solutions, identifying risks greatly depends on subject matter expertise. Through experience and foresight, your precision automation partner can identify when specific events are triggered that cause specific problems.
The first deals with source analysis (internal and external), while the latter deals with the threat analysis. Identification begins with developing a detailed User Requirements Specification (URS) at the very beginning of a project. The URS details what the user (or client) expects the solution to do by focusing on one requirement at a time, specifying what each requirement can do in a concise and precise manner, making sure that it is testable when the system is built, and traceable through the life cycle.
From the URS, the Functional Requirements Specification (FRS) is born, where we, as your solution partner, agree to provide the capabilities specified, in specific ways, to satisfy the URS. Instead of jumping into project execution, time well-spent developing a thorough user requirements helps enormously in proper risk identification, thus avoiding exponentially increasing delays and cost implications. The most common and generic risk we face in precision automation is when the process to generate the URS and FRS has not been thoroughly vetted. Risk identification should be an integral part of the planning process.
Step 2: Prioritization
Prioritization takes place by identifying the risks with both the highest probability and impact, in order to focus on them first. Risks with lower probability and/or impact are handled in descending order. Furthermore, failure to properly identify these high risks and following the high-risks first method can often result in lack of proper deployment of resources and poor project execution.
Step 3: Resolution
Resolution, or risk treatment strategies, is neatly summarized by SARA (Share, Avoid, Reduce, Accept).
- Share or transfer risk mitigation to a third party, such as a consultant, specialist, or sub-contractor
- Avoid by changing approach
- Reduce probability or negative impact by taking intermediate steps
- Accept the consequences
Recent developments in Rapid Prototyping (printed polymers, sintered metals, etc.) have wildly revolutionized our capability to characterize the real magnitude of any identified risk, in record time – record time is what automation is about. Being able to leverage proprietary platforms, such as the DWFritz Flexible Platform (DFP 5000 or DFP 1000) or High Volume Metrology (HVM) allows DWFritz to get critical results while vastly improving capabilities, such as:
- Precision part-handling.
- Cosmetic defect detection (scratch, dent, or adhesive squeeze out).
- High-speed, in-motion metrology.
Step 4: De-risking via Proof of Principle
Creating Design of Experiments (DoE) or Proof of Principle (PoP) studies with recommended technologies offers an opportunity to iterate multiple times within previous single-iteration machining timeframes, thus creating better solutions that reduce risk in a project. Agile Project Management methods also offer a proven way to constantly adapt to developments on risk mitigation, making progress a constant, regardless of roadblocks.
One medical devices client, for example, came to us with a very challenging problem, requiring an automated method of manufacturing embolic coils. To de-risk the project, we embarked on a PoP study to develop several key innovations to better understand how we could manufacture such a complex product in volume.
Clients hire precision automation partners to not only solve their advanced manufacturing challenges, but also to mitigate risk. The process of identifying, prioritizing, and resolving risks requires a great deal of expertise and experience, which makes selecting a precision automation partner such as DWFritz the most critical step in the process.