The popular narrative surrounding 3D printing generally focuses on rapid prototyping and manufacturing end-use products, but these stories overshadow one of this technology’s greatest benefits in the world of metrology: Creating inspection fixtures.
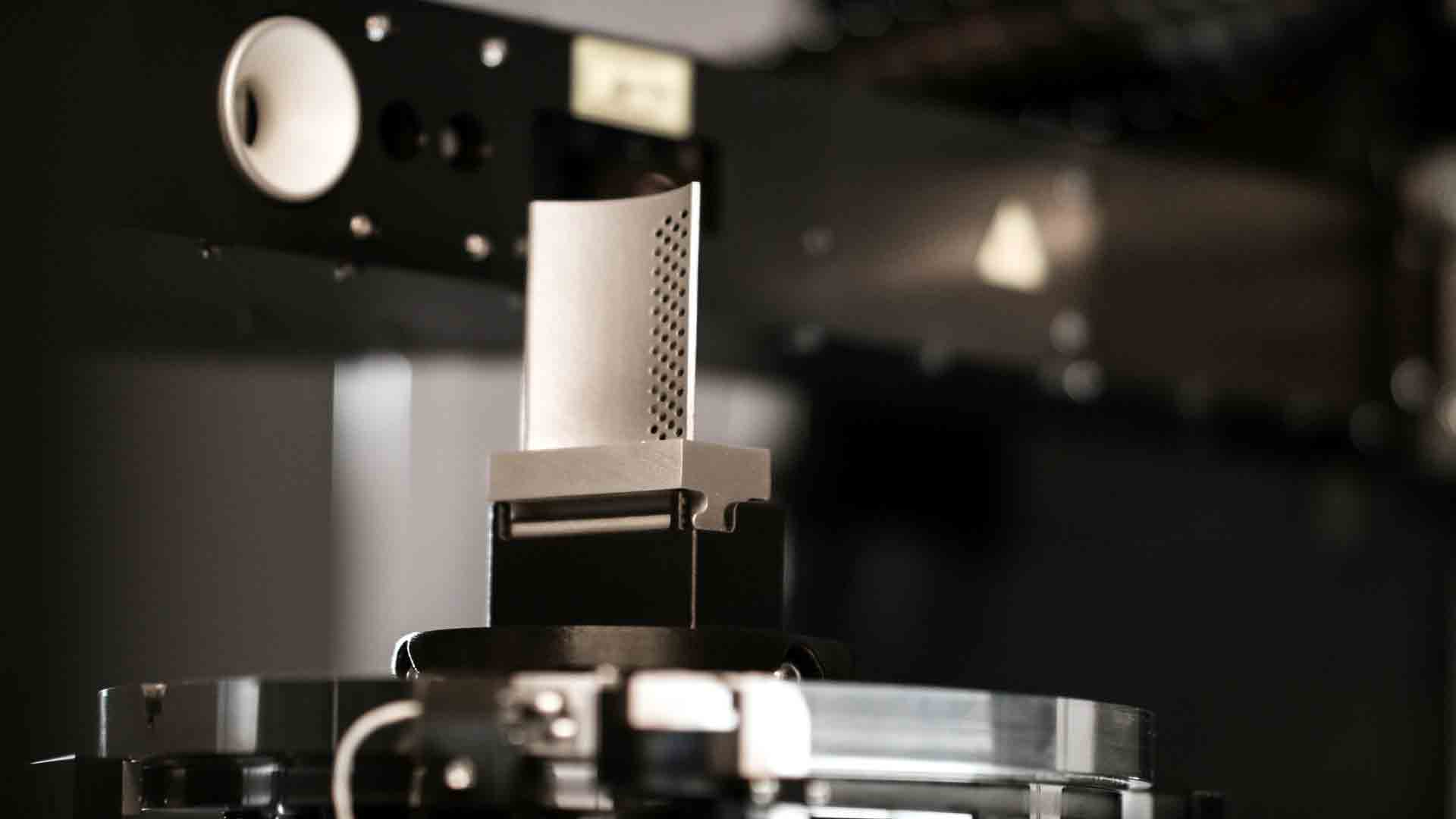
Fixturing may not be the most fun topic in metrology, but they are an important element in any metrology application be it off-line, near-line or in-line. Across manufacturing industries, coordinate measuring machines (CMM) are used alongside other metrology systems to measure parts. For accurate, repeatable, and reproducible results, CMMs use machined fixtures to secure the parts position rigidly at the optimal angles for inspection, minimizing variance and ensuring consistency.
Conventional fixtures, which typically include standard inspection components such as grid plates, columns, clamps, and standoffs, may cost more than $1,000 for basic options – and are still not a drop-in-place solution. For critical parts, companies are known to invest thousands of dollars in fixturing. Several versions of a fixture are often required for parts that vary in size, and parts with complex architectures often require equally complex fixtures. Such specialized fixtures can be outsourced or machined in-house, but both options are costly and time consuming.
DWFritz’s ZeroTouch® non-contact metrology platform minimizes the constraints traditional CMMs face with machined fixtures by leveraging 3D-printed guides. Using advanced imaging techniques, ZeroTouch orients the part virtually – in nearly any placement configuration within the measurement envelope. Once captured, software identifies the part and its orientation to define a virtual reference datum. A dynamic compensation file makes necessary corrections for each single point measured in the direction of the surface, which establishes the part coordinate system relative to the machine.
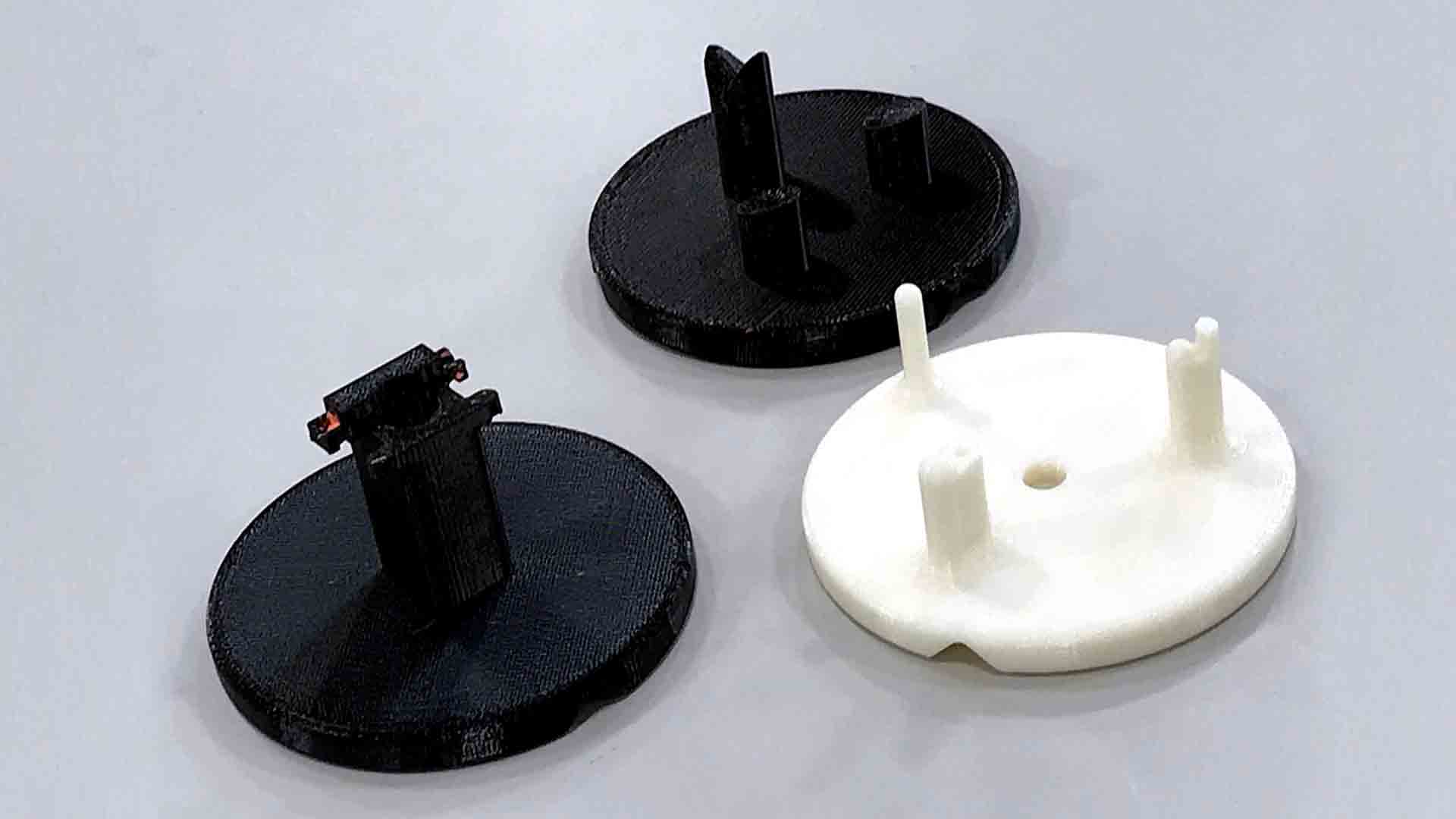
In the case of ZeroTouch, a 3D-printed fixture is designed to match the part quickly and with sufficient accuracy that the part can be placed or fastened to the guide and situated on the measuring platen for data capture. Guides are typically 3D printed on a fused deposition modeling (FDM) 3D printer that uses a continuous filament of ABS (acrylonitrile butadiene styrene) plastic material. The turnaround time to produce a 3D-printed fixture will vary depending on the size and complexity of the fixture, as well as the printing process and equipment used.
Complex component guides can be built in a fraction of the time required for machined components, and for pennies on the dollar compared to traditional methods. Guides created in CAD with relative ease can put a 3D-printed design in an employee’s hand within a day, significantly improving productivity. The speed and ease of turning around 3D-printed guides supports rapid prototyping and testing of innovative ideas. Design is an iterative process, and 3D-printed guides allow you to rapidly test ideas for various part at a much lower cost than with machined fixtures.
Further, unlike traditional fixtures, 3D-printed guides can be expendable. Manufacturers consider machined fixtures an asset that must be stored, catalogued, and maintained for future use; 3D-printed guides do not require the same care and feeding, potentially saving companies a healthy sum on storage and maintenance alone. A 3D-printed guide that breaks, falls out of tolerance, or is no longer needed and discarded can be quickly and easily replaced. Furthermore, in low-volume, high-mix part environments, such guides find great applicability.
Learn more about ZeroTouch®, a high-speed non-contact multipurpose metrology platform that simultaneously measures multiple part features and complex geometries as well as surface topology.